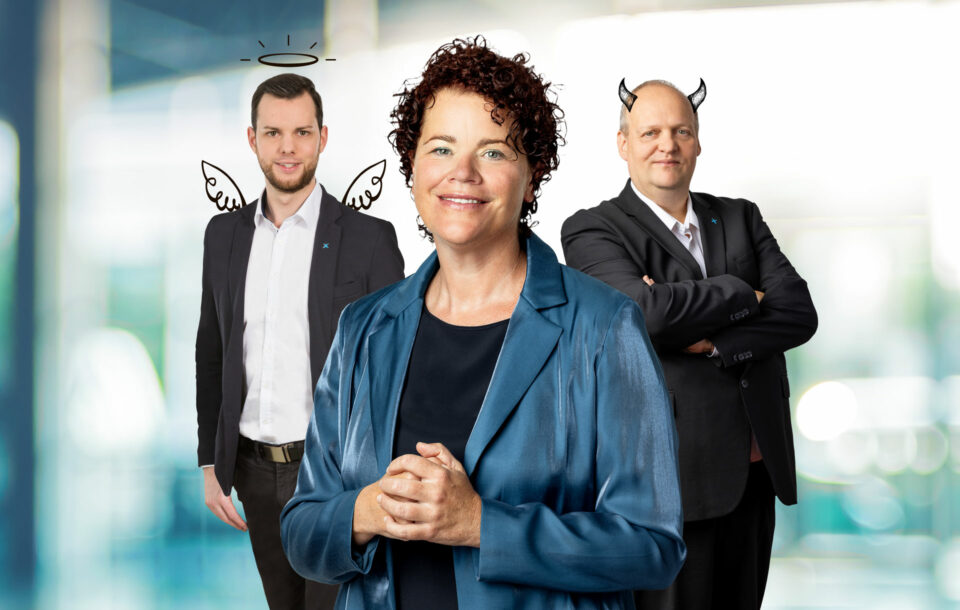
On the 11th of March 2025, our hybrid change:maker & work smarter event was transformed into a laboratory of processes. Using water, waffles and gummy bears, we worked together to uncover both the obvious and hidden pitfalls of supposedly efficient business processes.
Processes are the invisible backbone of any successful business. But what happens when that backbone is weak? Our experts Armin Buchner and Gaston Saborowski took the participants on an interactive journey through the biggest types of waste that can lurk in almost any process.
When processes become a challenge
The evening began with a dynamic discussion among the participants. Confessions of their own process sins revealed a familiar pattern:
- Processes that exist but are not followed
- The procrastination trap: processes that never see the light of day due to a lack of drive
- Processes that fall victim to a love of detail
- Overly complex processes that fail due to their own complexity
- The fine line between theoretical concept and practical implementation
The 7 ‘deadly’ sins of a process at a glance
- Rework: When mistakes lead to more work
- Movement: Inefficient ways and processes that waste time and energy
- Transport: Information and material flows with risks
- Inventory: Buffering of resources
- Waiting: Delays due to bottlenecks and approvals
- Overproduction: Flow of resources without corresponding benefits
- Overdevelopment: Too much regulation that threatens acceptance
An experiment that mirrors our process world
What do waffles, jelly babies and drinks have to do with processes? More than you might think! In an entertaining setting, the 7 'deadly' sins were brought to life using processes from the catering industry. With an improvised bar and brave volunteers from the audience, our experts turned abstract process issues into tangible experiences.
Process: Serving water
The 'water glass experiment' showed how perfectionist expectations and unrealistic time targets lead to mistakes and inevitable rework. Fill a glass in exactly one second and serve it flawlessly? What sounds simple in theory fails in practice.
The balance between sensible pre-production and waste of resources was then demonstrated. Too many filled glasses that could not be sold highlighted the problem of overproduction. Finding a sensible compromise remains one of the biggest challenges in process management.
Process: Distributing waffles
The 'waffle experiment' revealed classic challenges in movement and transport processes. The communication chain broke down when orders had to be passed on and personalised. Instead of efficient processes, there were detours and misunderstandings. Scenarios like this are a daily drain on time and resources in many companies. The participants also quickly realised that the process required too much movement and suggested alternative solutions to increase efficiency.
Process: Delivering jelly beans
In the 'jelly bean experiment', an improvised call centre, impatient customers and a regular customer with special rights demonstrated how quickly a process can lose its traceability. The regular customer pushed forward and threw the whole process off balance. How often do companies throw established processes overboard for perceived exceptions, only to end up creating more chaos than benefit?
The eternal tension between waiting time and quality became particularly apparent when the shop had to close at 6pm while customers were still queuing, leaving them empty-handed.
In the end, the vicious circle came full circle with the realisation that not everything needs to be reinvented. It is often enough to optimise existing processes and use existing resources wisely. The solution does not necessarily lie in new tools or complex structures. What ultimately counts is the content of a process.
From practice for practice: When your own process stalls
Ironically, our presentation itself provided an unintentional lesson in process management. We ran over time and not all of the key insights were as clear as we had hoped. Proof that even process experts are not immune to the pitfalls of complex workflows, and that every process requires continuous improvement.
Paradoxically, this underlined a central message of the evening: reconciling theory and practice is not as easy as one might think. And it is precisely this tension that makes process management such a fascinating challenge.
The conclusion of our experts
Absolute avoidance of one or more of the seven types of waste in the process is neither possible nor sensible. Our experts Armin Buchner and Gaston Saborowski emphasised that process optimisation should not be a race to perfection. The types of waste are intertwined. Those who aggressively fight one sin often provoke another and risk the most dangerous sin of all: overdevelopment of the process, which inevitably leads to a loss of acceptance on the part of employees.
Successful process management requires time for reflection, interaction with all stakeholders and the courage to change. The key is a balanced mix of structured process management and flexible change management.
Their advice for a good, practiced process:
Allow yourself a few sins. Look at your processes from different perspectives, such as quality, cost or industry. Define clear priorities and involve your employees in any adjustments. Because both angels (optimisation) and devils (waste) give your process its identity and thus lay one of the foundations for the sustainable success of your process management.